Tag: Incense
With the upcoming launch of our Footpatrol Gasmask Incense Chamber, we sat down with Julien from Batch.Works who helped us create the first part of the puzzle for the chamber. Julien sat us down to talk us through the unique processes of 3D printing and the challenges that came with turning the iconic 2D Footpatrol Gasmask into a 3D object.
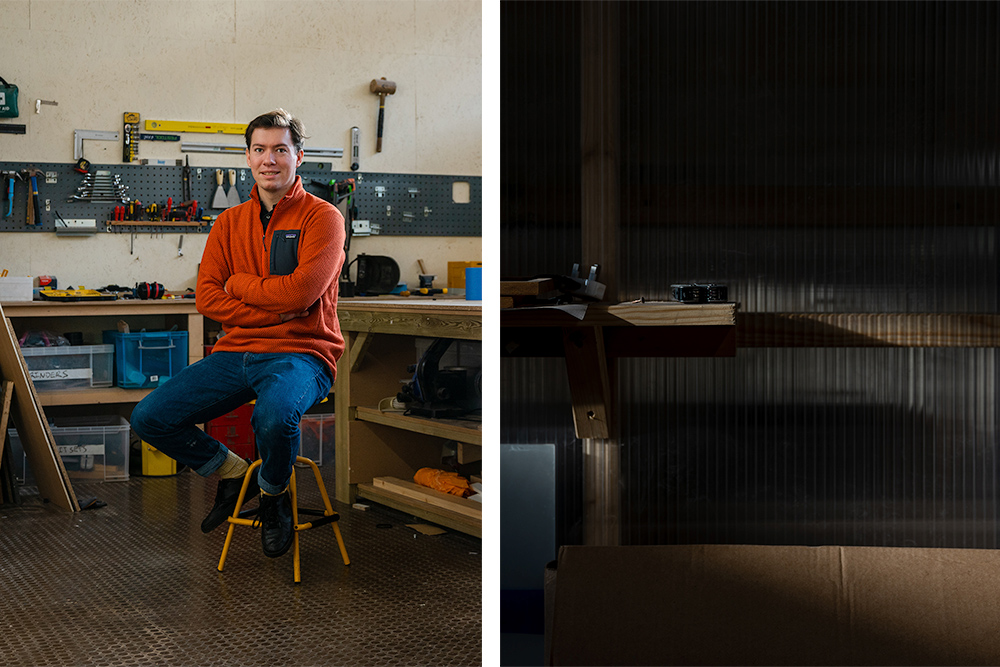
Footpatrol: Julien we are super excited to be here! How are you?
Julien: I’m great thank you! Super excited to finally launch this collab! But also pretty tired as it’s the busiest time of year for Batch.Works and we are opening a new fabrication hub in Amsterdam this month…
Footpatrol: What you guys do is something I must say I don’t know a lot about. Can we get a little insight into Batch.Works, yourself and what got you into creating such an individualistic fabrication process?
Julien: I was trained as an architect but I’ve always been passionate about making and fabrication processes. I’ve been fascinated about the possibilities of 3D printing for about a decade and I’m still amazed about the versatility and power of this technology.
I created Batch.works in 2018 with the mission to utilise 3D printing to enable a sustainable and speedy alternative to traditional product development and production.
We are also proud to be using exclusively 100% recycled material from our partner Reflow in Amsterdam.
Footpatrol: Were there any creatives that inspired you into following this path?
Julien: I’ve been inspired by many creatives along the way starting with Architects then followed by furniture designers. Bold Design, a french duo, was the first design studio I discovered to push the limit of 3D printing and make absolutely amazing pieces like the Hairy Vase. We are now working together on many projects and are part of the Batch.Works catalogue.
Footpatrol: In terms of concepting design ideas, how do you and the team go about that?
Julien: We have different approaches depending on the request but as we are a manufacturer, we have a strong focus on production and practicality on how we are going to make the end product so when a brief comes to us we quickly dive into design for manufacturing with the client.
Footpatrol: It must be such a great feeling seeing these designs come to life in the way that they do?
Julien: YES! That’s the beauty of 3D printing, bringing amazing pieces of digital product or art to life. Especially in this collab, starting from a 2D logo to a full model was very incredible.
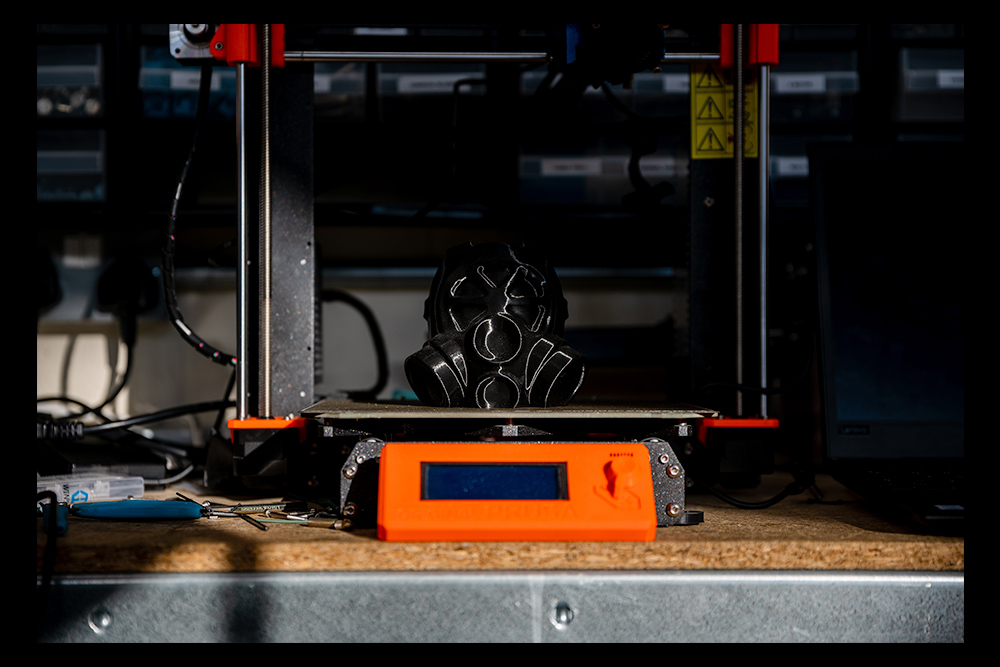
Footpatrol: I know you guys have worked with all sorts of places from the Tate to WHSmith. Could you tell us a bit about what these projects entailed and how they came into fruition?
Julien: We’ve been involved with quite a few project recently! The Tate is part of the Tate edit selection, they have shortlisted a number of London based creatives to sell their project and we are really excited to be part of it!
With WHSmith, we recently received a grant from the Mayor of London to work closely with them to turn their waste into a collection of product which will be released early next year!
We also have other exciting project with BENE, a furniture brand and the opening of our Amsterdam Hub which will allow us to produce in the EU as Brexit has been a big hit for us.
Footpatrol: Of course we are here to talk about our project together! How has it been piecing it all together?
Julien: It has been a long but amazing journey, the project started over 2 years ago! The global pandemic gave time for the project to take shape and mature. In March/April 2019, Asheeba and John came to me with a brief to bring the Footpatrol logo into an incense chamber. As a 3D printing company, everything is possible! We quickly realised the complexity of bringing a 2D logo into 3D shape would be challenging. Thanks to the previous collaboration Footpatrol did with Duffy for the ring, it really helped us to make up the part of the logo that doesn’t exist. After many iterations and prototypes we finally managed to bring the perfect model to life.
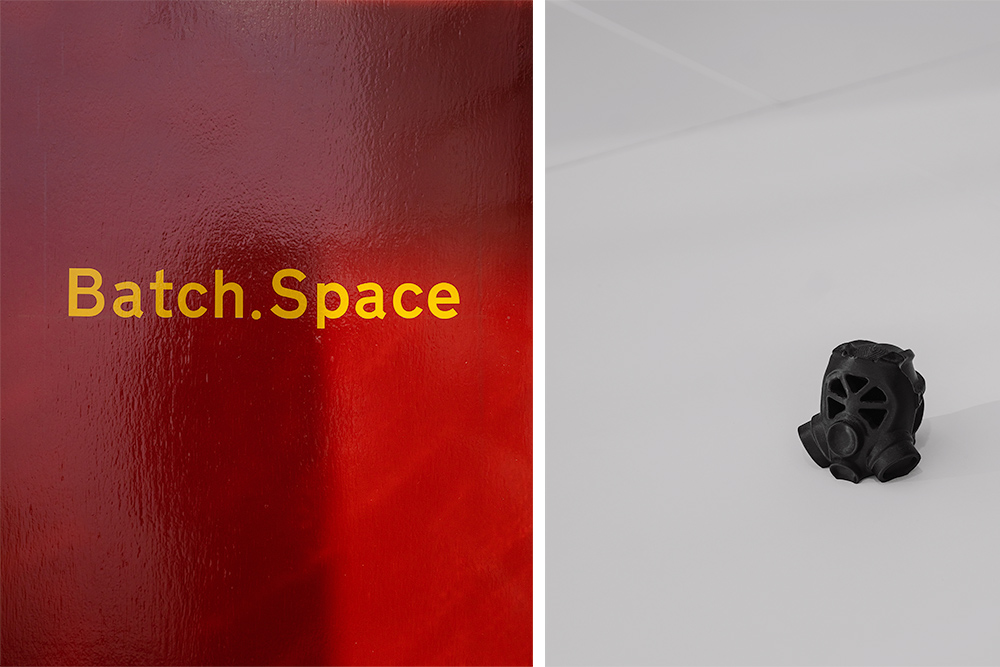
Footpatrol: Is it your first time creating an incense chamber?
Julien: Definitely yes, this is not something that comes through the door very often! It’s also why we got very excited about this challenge and project.
Footpatrol: Were there any unexpected challenges in the design and manufacturing process?
Julien: The biggest challenge was to produce the pieces. It was actually meant to be 3D printed in ceramic but with Covid hitting globally this was not an option anymore. We managed to partner with two wonderful young graduated ceramicists from Stoke-on-trent, Yunji Shin and Nicole Waefler. Many established professionals would not work on this piece due to the complexity of the model but Nicole and Yunji took on the challenge and the result is astonishing…
Footpatrol: Julien we really appreciate you letting us come down to the studio to see the behind scenes of the brand. Before we let you go, is there anything you would like to share to the Footpatrol reader and followers?
Julien: Thank you for coming down! Great pleasure to have you here and finally release this product! We’ve just opened Batch.Space in East London, next to Broadway market above a bus depot. It’s a place where people can make and connect with other creatives across many disciplines. It’s also Batch.Works home so anyone is welcome to come for a tour!
Limited to 100 pieces, the Footpatrol Gasmask Incense Chamber will be launching in-store and online on Saturday 4th December priced at £100.
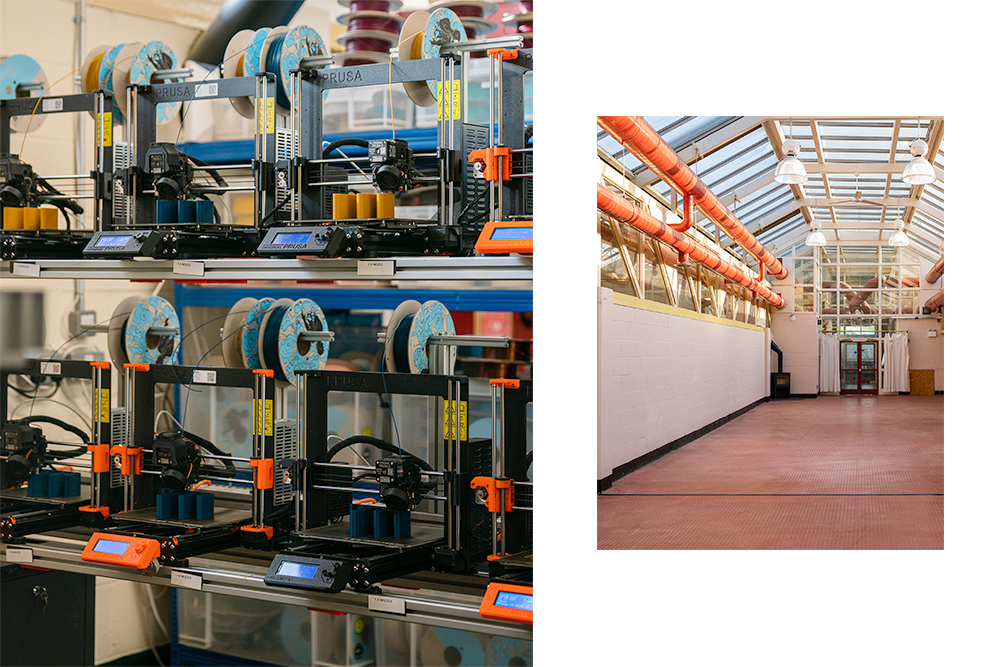
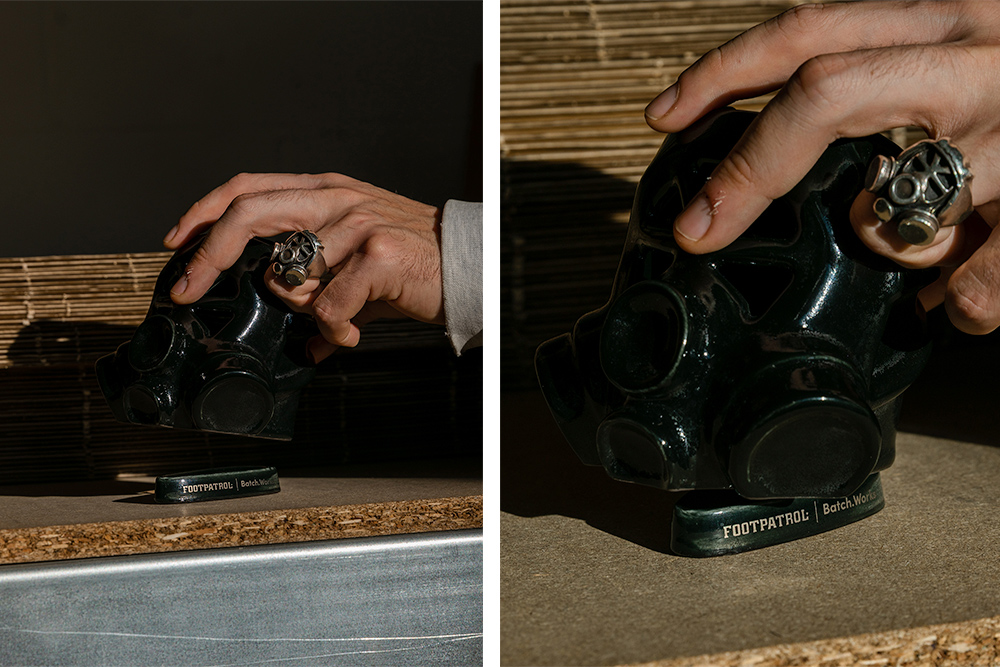
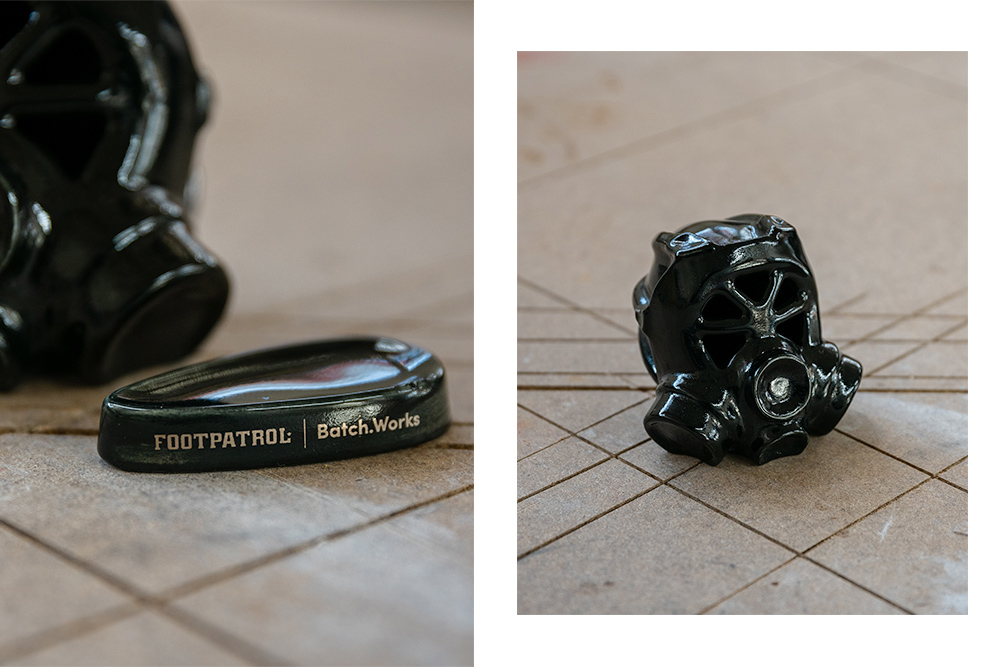
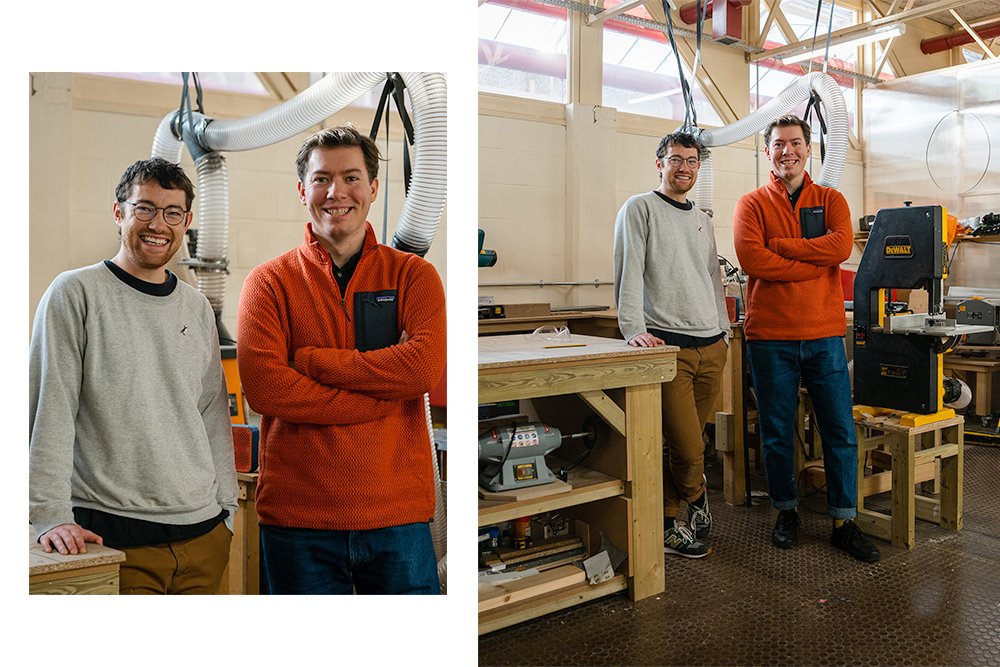
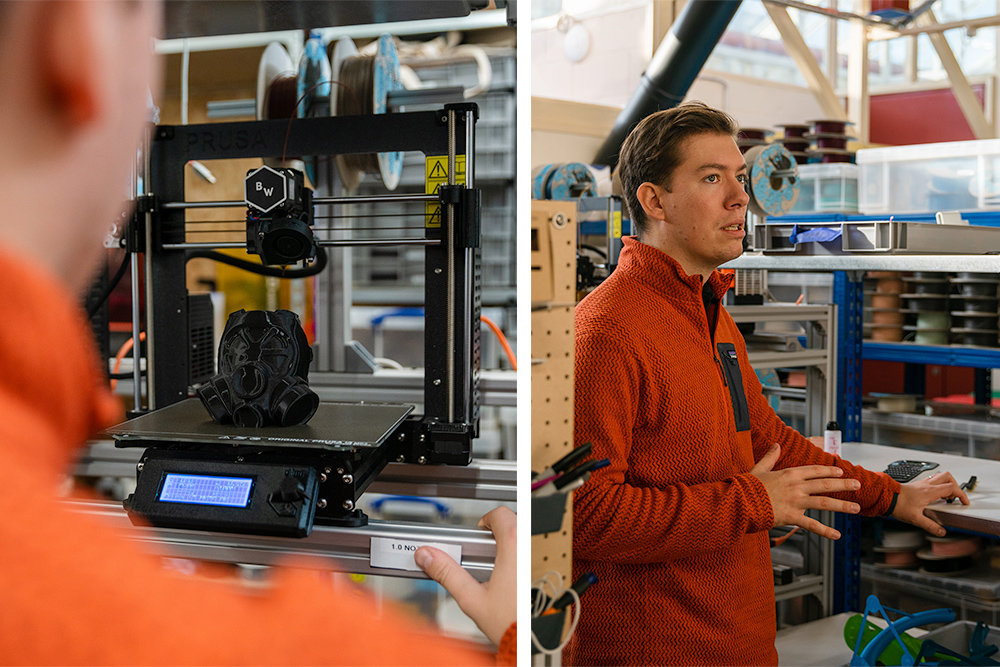
Over the years at Footpatrol. We have worked on a range of accessories, from keyrings, door keys, jewellery and even homeware pieces. Our interests outside of Footpatrol span far and wide which is what brings such diversity in our projects and collaborations.
To further broaden our horizons. Footpatrol have teamed up with 3D printing specialists, Batch.Works and fragrance experts, Earl of East to bring to you a Gasmask inspired Incense chamber and special Footpatrol incense to pair alongside it.
Earl of East was founded in 2014 as a shared passion project between Niko Dafkos and Paul Firmin. Since launch it has grown into a business built around a love for fragrance. What started as 3 candles soon developed into a whole range of lifestyle and beauty products.
To best showcase the work Earl of East produce, we partnered up to produce Footpatrol scented incense composed of a balanced blend of cedarwood & jasmine essential oils. The aim was not only to create a scent that helped alleviate stress, anxiety and heighten your mood turning your home into that happy place we all like to keep tucked away in our minds.
Based in East London, Batch.Works have been pushing the realm of 3D printing by turning it into forms that fit perfectly within households. Using the latest technology Batch.Works have focused their attention on being able to produce in an eco-friendly way ensuring the materials they use are recycled and responsibly sourced either from sugarcane starch or recycled packaging.
From turning our prestigious Gasmask logo into a 3D printed item, the team at Batch.Works worked closely with Nicole and Yunji, a duo of emerging ceramicist talent who worked meticulously by hand to create a limited run of ceramic Black incense chambers using the 3D printed model as the original mould.
Simply place a lit incense cone on the base within the chamber and watch as the smoke drifts out of the openings within the Gasmask chamber.
Limited to 100 pieces, the Footpatrol Gasmask Incense Chamber and Incense Cones (sold separately) will be launching in-store and online on Saturday 4th December (Available online from 08:00AM GMT), priced between £20 – £100.
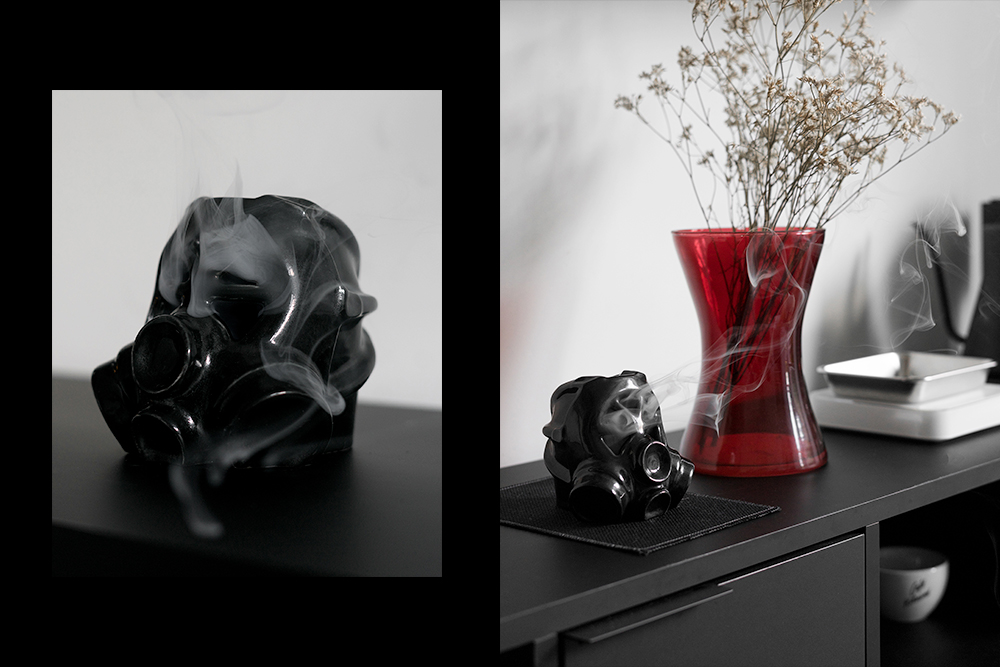
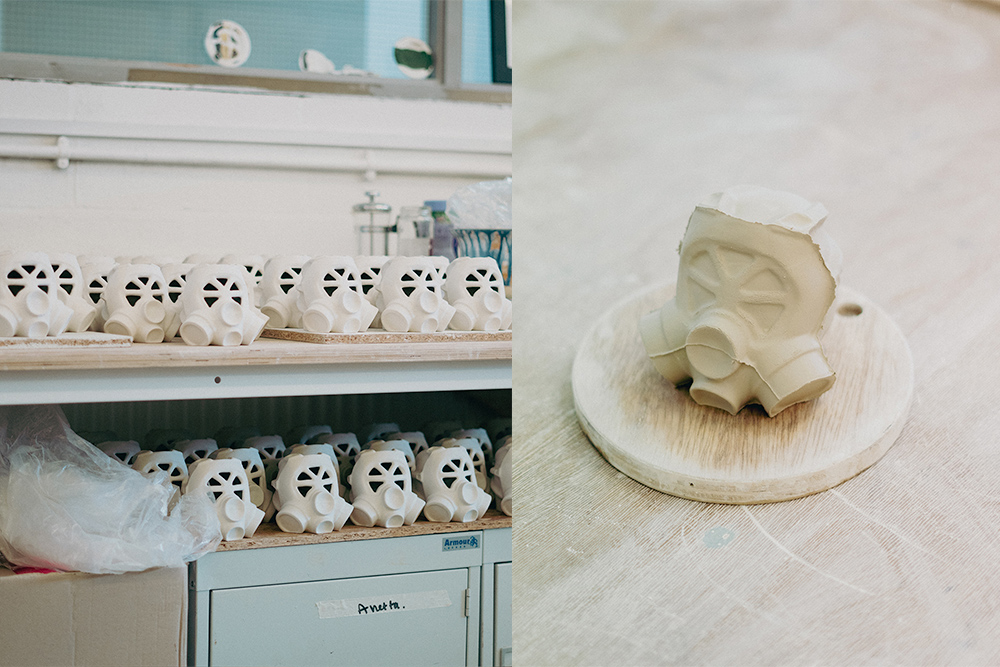
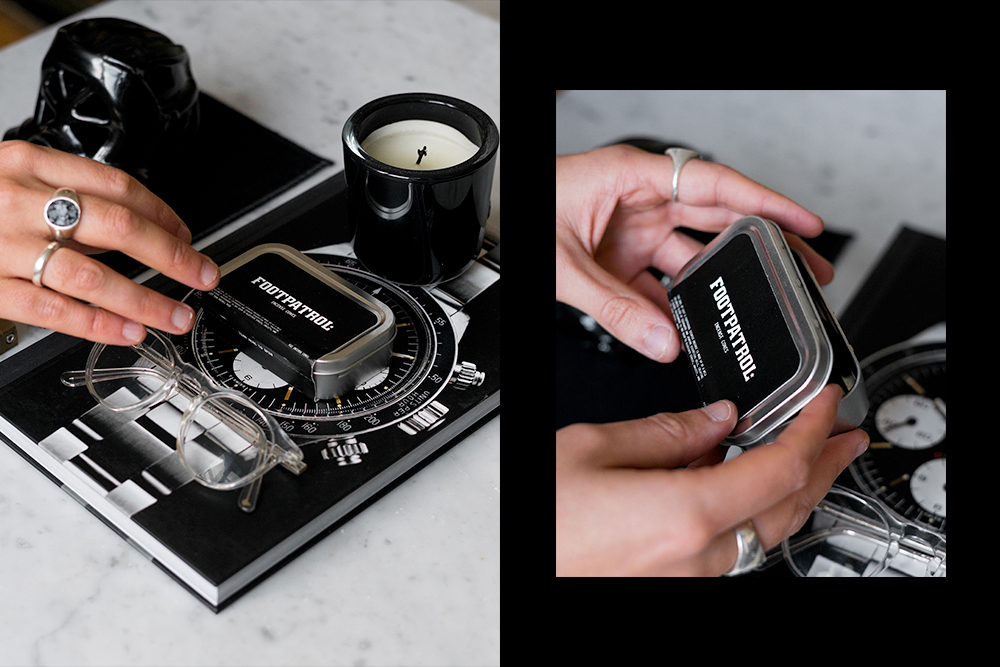
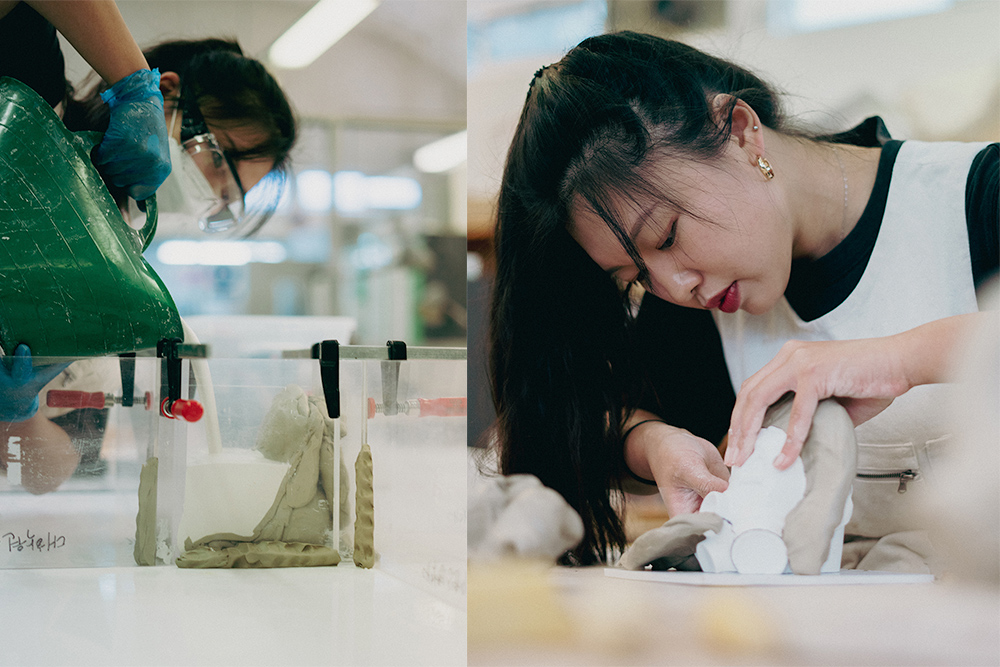
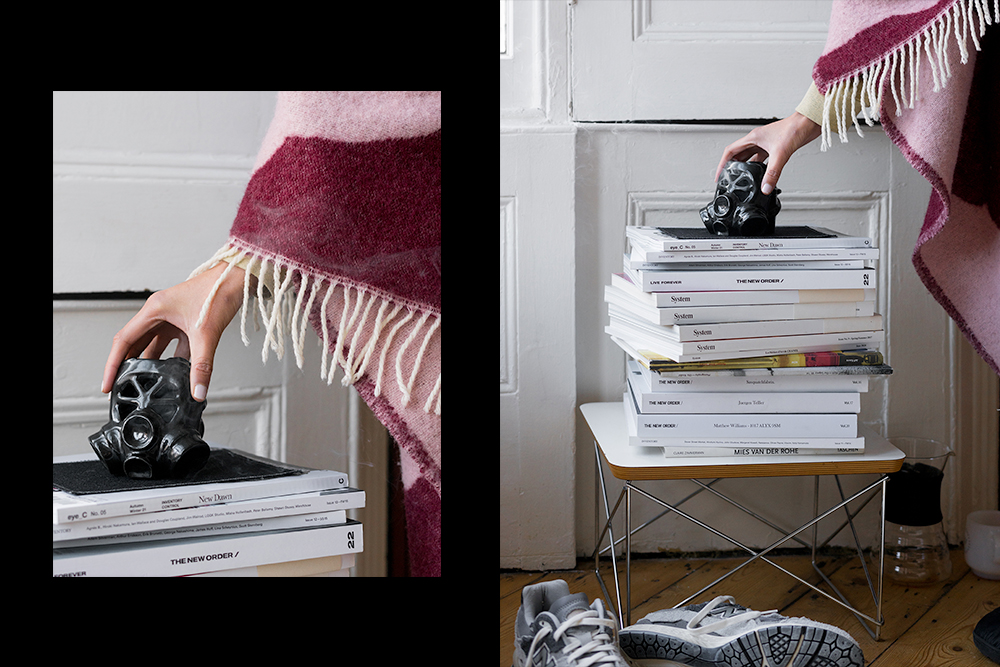
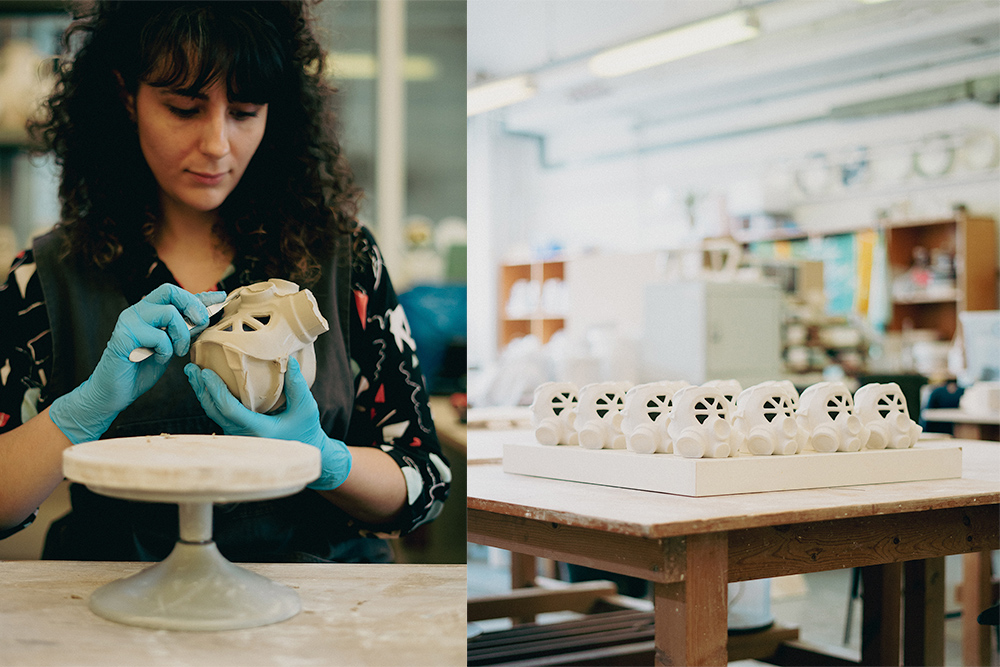

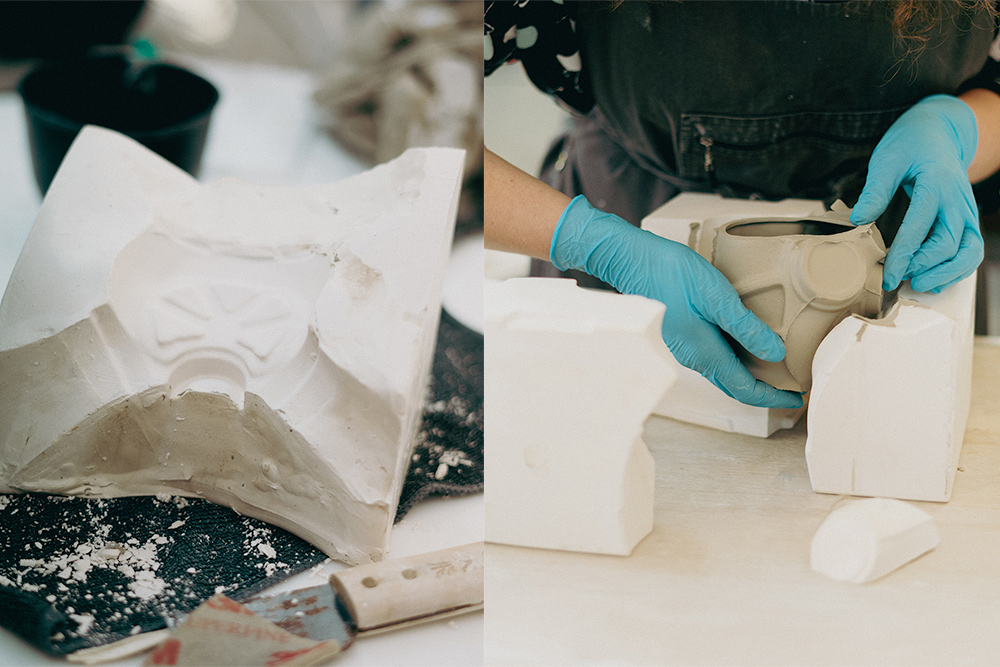
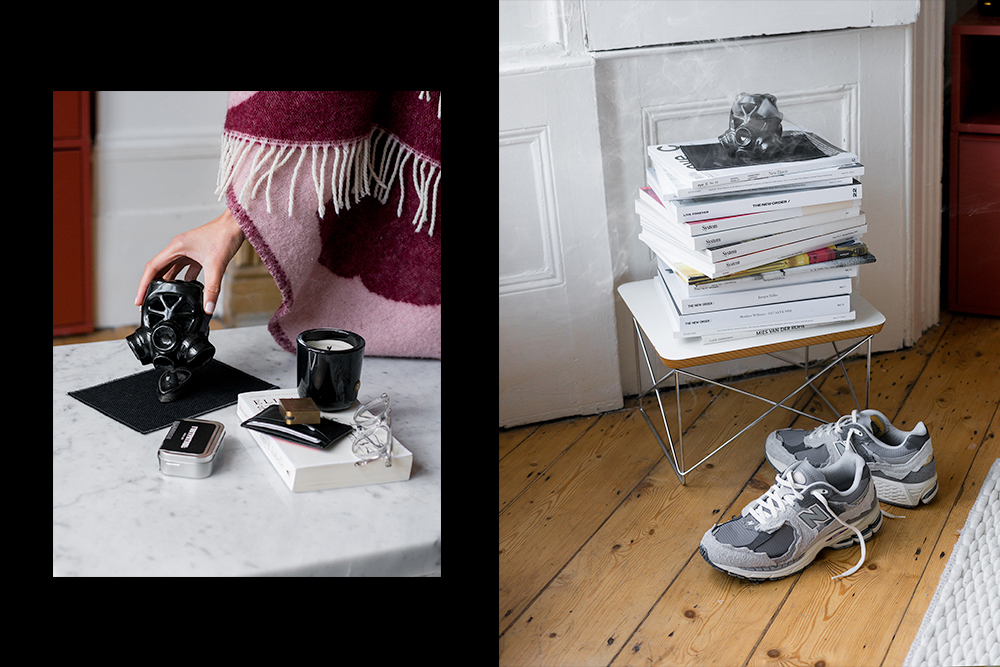
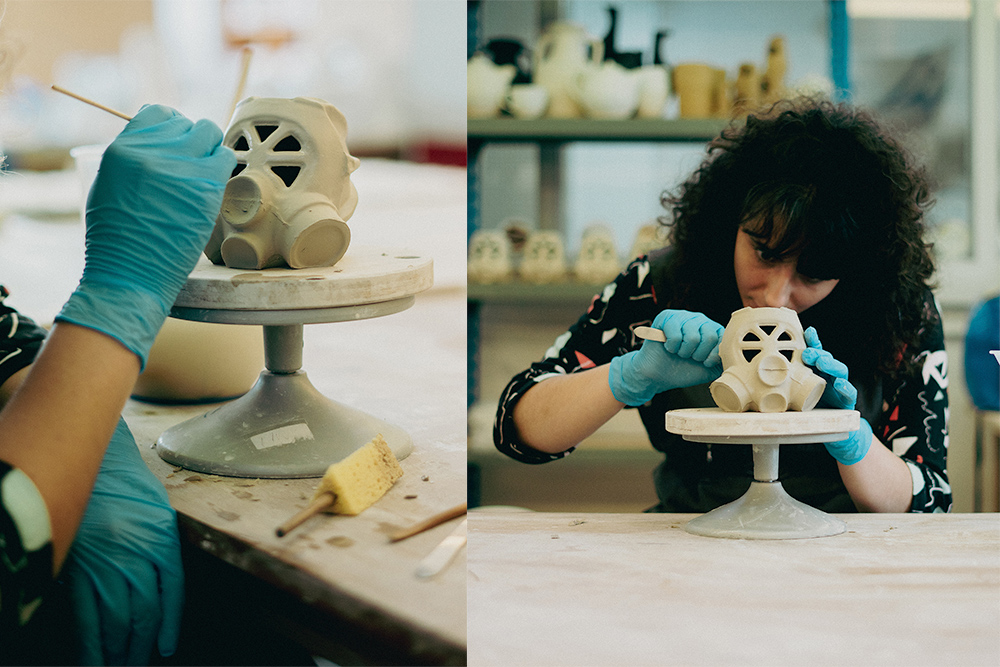
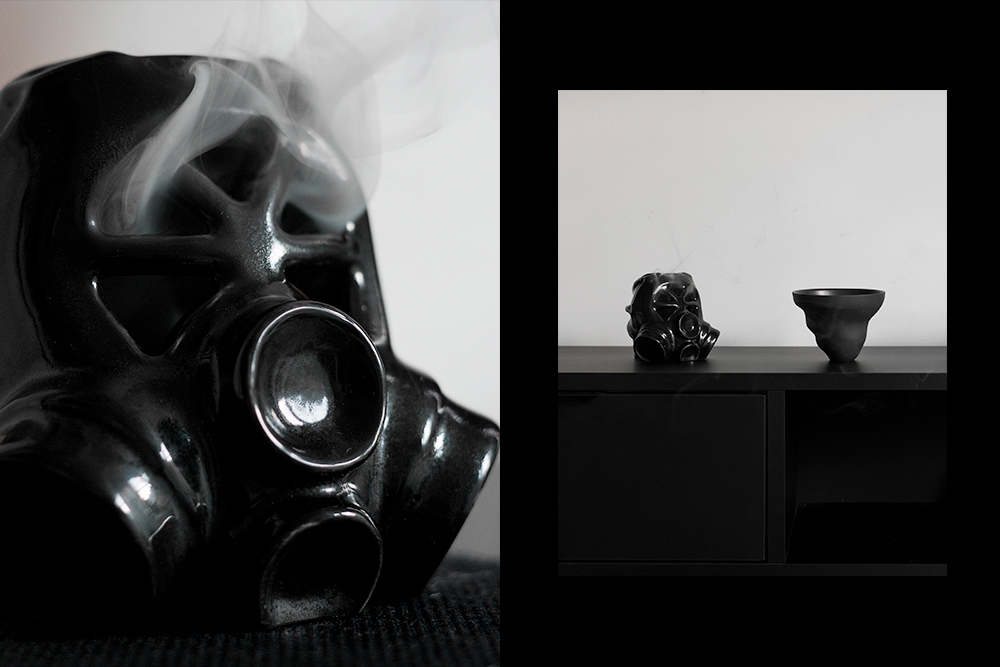
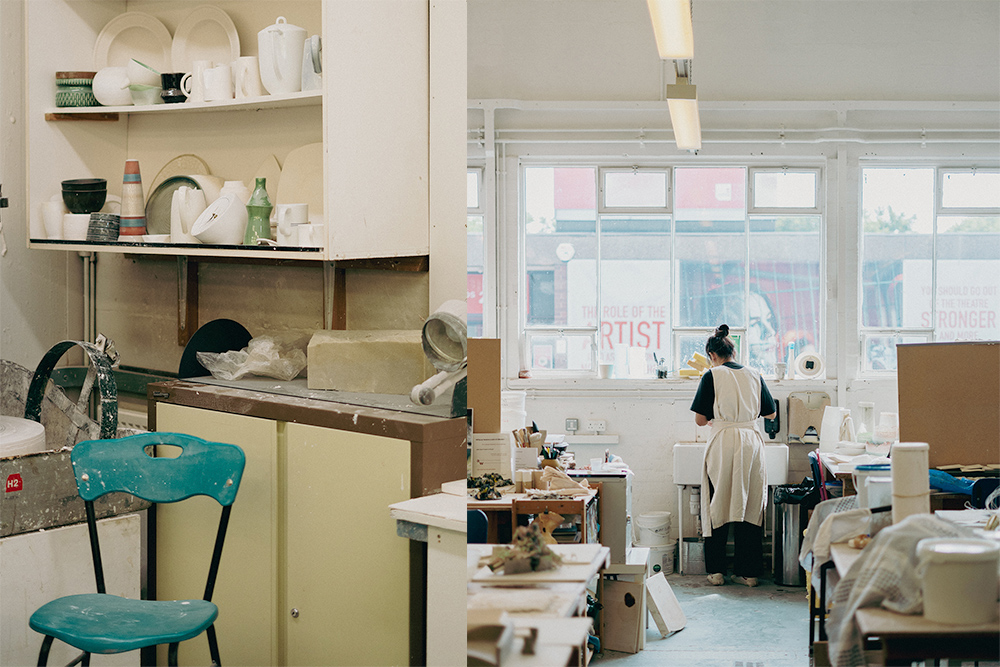
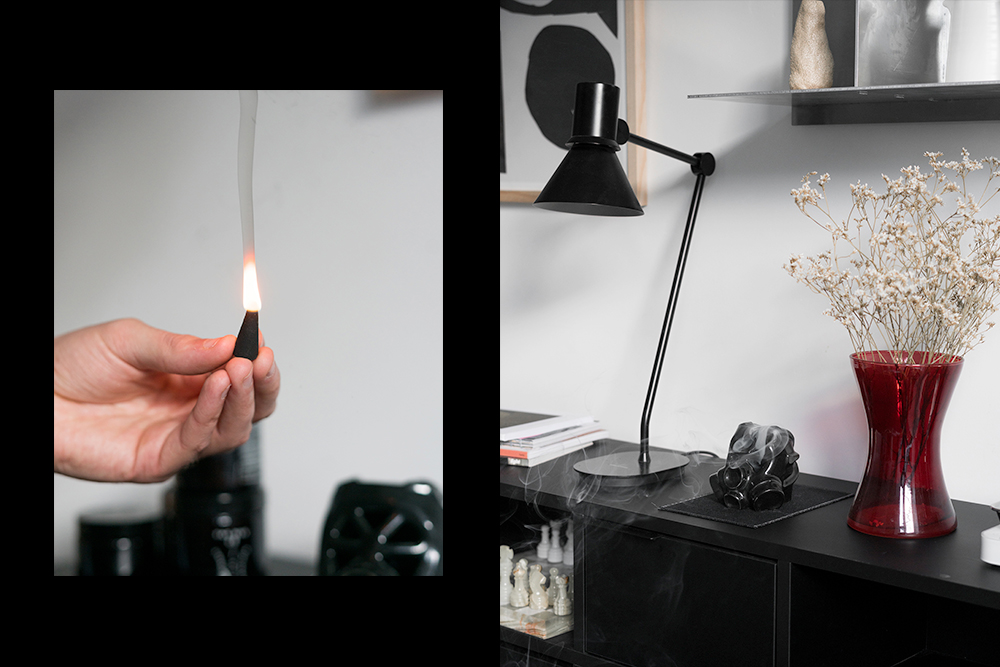
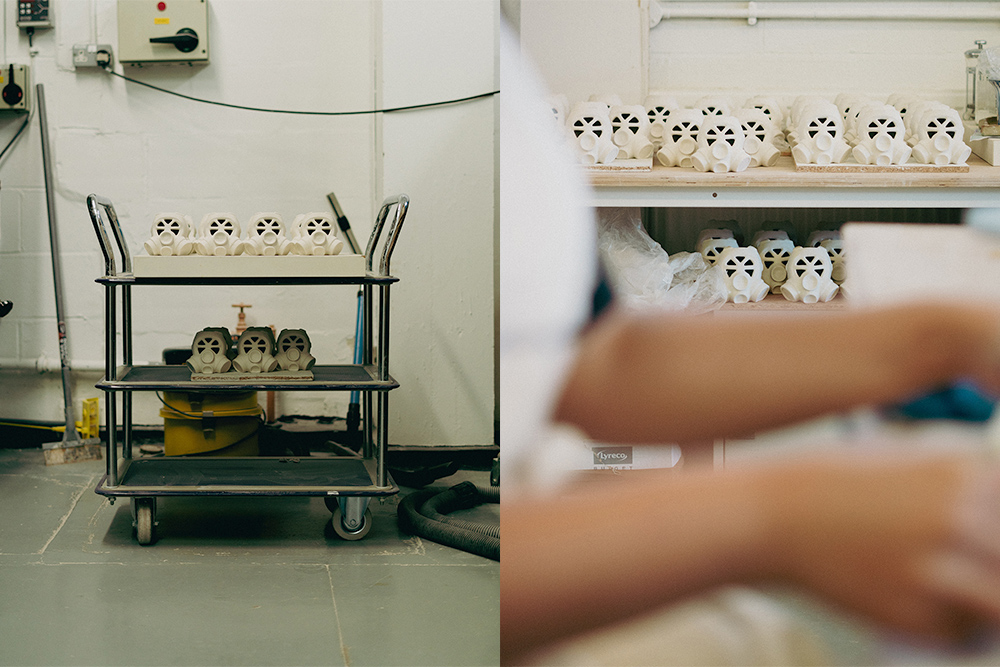
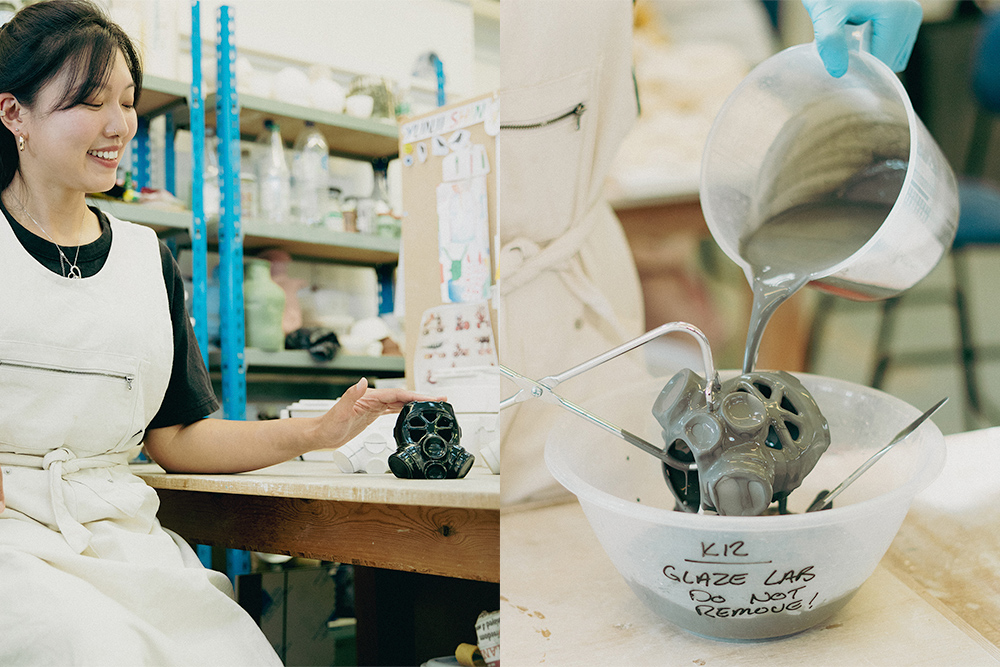
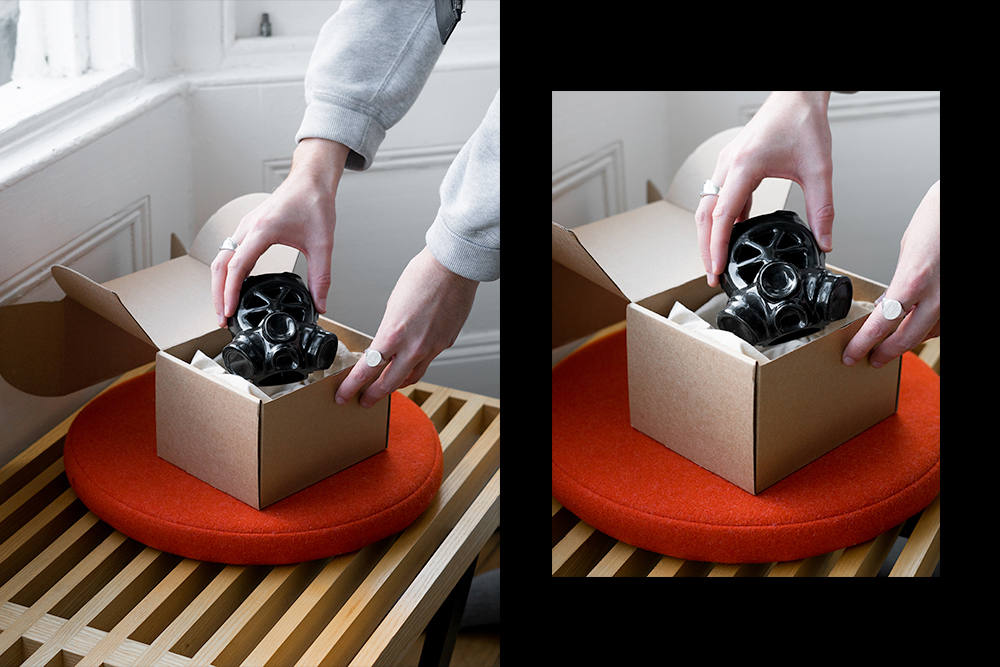
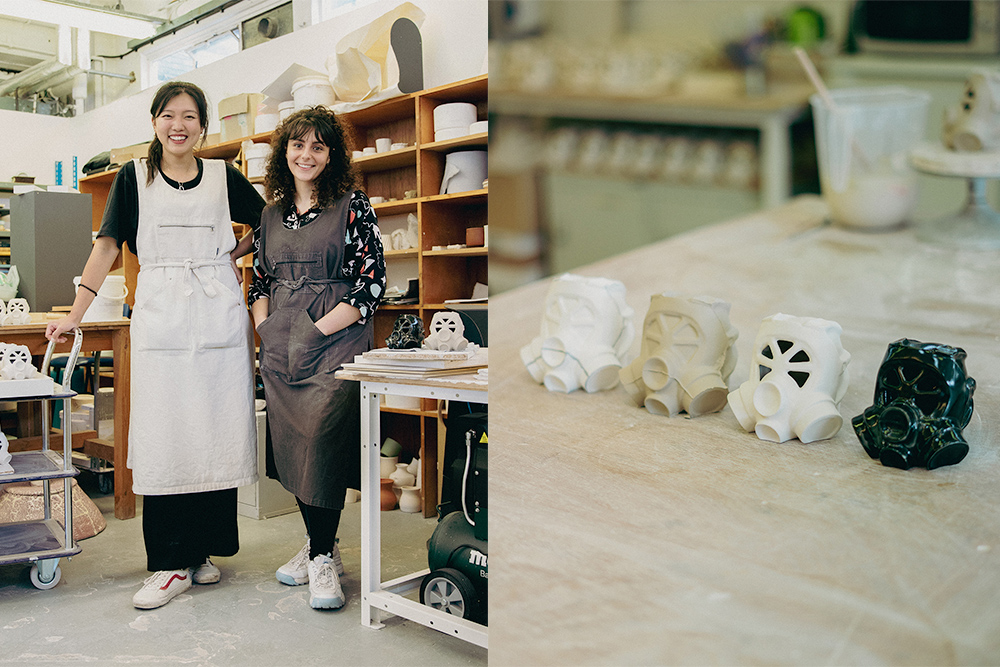